- Product Description
Computer Automatic Hydraulic Universal Testing Machine
1.Matters need attention
Please read this manual carefully before using this equipment, and keep it for future reference purposes
The installation environment requirements
① Environment temperature 10 ℃ ~35 ℃
② Relative humidity of not more than 80%
③ No vibration, no corrosion, no strong electromagnetic interference environment
④ The levelness should be no more than 0.2mm/1000mm
⑤ There should be around 0.7m space, equipment must be reliably grounding.
Power requirements
This equipment use 380v three-phase four-wire (in addition to the other tips) alternating current (AC), voltage stability, do not exceed ±10% of the rated voltage,the allowable current of the sockets shall not exceed 10A.
Hydraulic oil requirements
The equipment adopts standard hydraulic oil as the working fluid: when the room temperature is higher than 25 ℃ ,using No.68 anti-wear hydraulic oil . when the room temperature is below 25 ℃ ,using No.46 anti-wear hydraulic oil.
In winter, when the room temperature is too low, after turning on the machine please preheating equipment (start the oil pump motor) for 10 minutes. When frequent using, hydraulic oil should be replaced half a year, whether the fuel tank and filter should be cleaning or not is decided by the pollution degree .
This equipment can not use engine oil, gasoline or other oil for instead. Failure of the hydraulic component due to the improper Oil , will not be included in the scope of warranty.
About the emergency stop
In case of an emergency in the installation, operation, such as solenoid valves can not release, abnormal operation of motor, which may causes damage to the machine or injury of tester, please turn off the circuit breaker.
Precision
Equipment is exactly calibrated before leaving the factory, do not adjust the calibration parameters. Measurement error increases due to unauthorized adjustment for the calibration parameters, will not be included in the scope of warranty. You can contact with local quality supervision department for calibration according to the equipment marking accuracy class.
Maximum force
Determine the measuring range of equipment according to the equipment label, measuring range is adjusted in factory, do not alter the range parameter, adjustment of the range parameters could result in equipment output force is so large that causes damage to the mechanical parts or output force is so small that can not reach the setting value, the damage of mechanical components due to unauthorized adjustment for range parameters , will not be included in the scope of warranty.
2.General introduction
WAW series electro-hydraulic servo universal testing machine
WAW series electro-hydraulic servo universal testing machine is based on GB/T16826-2008 "electro-hydraulic servo universal testing machine," JJG1063- 2010"electro-hydraulic servo universal testing machine," GB/T228.1-2010 "metallic materials - method of tensile testing at room temperature". It is a new generation material testing machine which developed and manufactured based on that. This series of testing machine is loaded with hydraulic , using the electro-hydraulic servo control technology for tensile testing, compress testing, bend testing,shear testing of metal and non-metallic materials,display a variety of curves,including stress, deformation, displacement and other closed loop control mode, can be arbitrarily switched in the experiment. It records and stores data automatically. It meets the GB,
ISO, ASTM, DIN, JIS and other standards.
The features of WAW series electro-hydraulic servo universal testing machine (type B):
① The test adopts microcomputer automatic control mode, with the functions of stress rate, strain rate, stress maintenance and strain maintenance;
② Adopt high-precision hub-and-spoke sensor to measure force;
③ Host which adopts four-column and double screws test spatial structure
④ Communicate with PC by high-speed Ethernet communication interface;
⑤ Manage test data by standard database;
⑥ High strength, high toughness and beautiful protective net for safety protection
4.Installation and commissioning
Prepare installation tools
Check the accessories attached to the equipment according to the packing list, and check whether the accessories are complete Prepare screwdriver, adjustable spanner and a set of inner six angle wrench
Fix the main engine
Fix the equipment according to the fixed parameters of the foundation with reference to the foundation drawing (see the parameters and instructions of the foundation drawing in the appendix of this manual for details) Unscrew the hose joint of the oil plug please safekeeping, in order to avoid the loss and caused the inconvenience of moving machine in the future. The connection must be closely, and pad into the sealing washer.
The oil circuit connection
Fill the right amount of hydraulic oil according to the mark on the oil tank (wait at least 3 hours before officially use after filling the hydraulic oil , to facilitate the bubble discharge in the hydraulic oil by itself), after filling the hydraulic oil connect the main engine and the control cabinet with hose in accordance with the sign (hydraulic jaw type requires jaw pipeline installation),when installing the pipeline,one gasket must be put between pipeline and splice , and fasten the joint by wrench, as shown The unscrewed oil plug of the hose please be safekeeping, in order to avoid the loss and caused the inconvenience of moving machine in the future. When moving the equipment please tear down the pipelines and seal them by oil plug closely.
Electrical connection
Take down the the whole set of data lines, in accordance with the data line corresponding with the interface on the control cabinet left . Please connect the power cord in strictly accordance with the attached label. The null wire (line 4) of the three-phase four-wire power line is strictly prohibited from wrong connection.
Open the computer package, install the computer (this step is only suitable for models which containing computer ); then install one end of the RS-232 communication line on controller, the other end install on the computer. Please do not replace the computer along with the equipment.(Tips:this step is not required for industrial computer type )
Open the printer package and install the printer according to the installation instructions attached to the printer (this step is only applicable to models containing external printer);After the printer is installed and connected to the computer, place it in a convenient location (the printer driver is saved on the local disk of the computer and needs to be installed by yourself) .
The first operation and commissioning
After electrical installation finished, switch on the power of the equipment, turn on the equipment.Use the control panel on the control cabinet or control box ,to rise the middle girder some distance (if the beam falls,you should immediately stop the operation and adjust the power phase sequence), then in accordance with the manual, operate the equipment with no-load, durning the rising of the worktable (can't exceed the maximum stroke),please observe if there is abnormal phenomenon, if it dose, you should uninstall and stop to check,remedy the trouble; if not, unloading until piston down to normal position, commissioning ends.
5.Operation method
Operation method of rebar test
① Switch on power,make sure the emergency stop button is pop-up,turn on the controller on the panel.
② According to the test content and requirements, select and install the corresponding size clamp. The size range of the clamp selected must include the size of the specimen. It should be noted that the installation direction of the clamp should
be consistent with the indication at the clamp.
③ Turn on the computer,log in software “TESTMASTER” and enter the control system, adjust the test parameters according to the test requirements(the using method of control system is shown in the "test machine software manual")
④ Open the fence, press the “jaw loosen” button on the control panel or the hand control box ,first to open the lower jaw, put the specimen into the jaw according to the test standard requirements and fixed specimens in the jaw, open the top jaw , press the “mid girder rising” button to rise the mid girder and adjust the position of specimen in the top jaw,when position is suitable close the top jaw.
⑤ Close the fence,tare the displacement value,start test operation(the using method of control system is shown in the "test machine software manual").
⑥ After the test, the data is automatically recorded in the control system, and set the printed content in the control system software for data printing(the setting method of printer is shown in the "test machine software manual")
⑦ Remove the specimen according to the test requirement,shut down the delivery valve and turn on the return valve (WEW series models) or press the “stop” button in the software(WAW/WAWD series models),restore the equipment to its original state.
⑧ Quit software, shut down pump ,shut down the controller and main power,Wipe and clean the residue on the worktable, screw and snap-gauge in time to avoid affecting the transmission parts of the equipment.
6.Daily maintenance
Maintenance principle
①Each time before starting the machine please check if there is oil leakage (specific parts such as: pipeline, each control valve, oil tank), whether the bolt is fastened,whether the electrical is intact; check regularly, maintain the integrity of its components.
② When finishing each test the piston should be dropped to the lowest position, and clean residue in time, worktable for anti rust treatment.
③ Operation after a period of time, you should have a necessary inspection and maintenance with the testing machine :clean the residue such as steels and rust on the sliding surface of the clamp and the girder ; check the tightness of the chain each half of a year; greased the sliding parts regularly, paint the easy-rusted parts with anti rust oil,remain cleaning and anti-rust.
④ Prevent from high-temperature, too wet, dust, corrosive medium, water erosion instrument.
⑤ Replace the hydraulic oil annually or cumulative after 2000 hours work .
⑥ Do not install other software in the computer, in order to avoid making the testing control system software run abnormally; prevent the computer from virus infection.
⑦ Before starting the machine you must check whether the connecting wire between the computer and the host and the power plug socket is correct or loosening, you can boot after confirmation of the correct.
⑧ Any moment cannot hot plug the power line and signal line, otherwise it is easy to damage the control element.
⑨ During the test, please do not arbitrarily press the button on the control cabinet panel, operation box and the test software.Do not rise or fall the girder during the test. Do not put your hand into the test space during the test.
⑩ During the test, do not touch the equipment and all kinds of links, so as not to affect the accuracy of the data.
⑪ Often check the level change of the oil tank.
⑫ Check whether the line connecting of the controller is in good contact regularly, if it is loose, it should be fastened timely.
⑬ After the test if the equipment is not used for a long time, please shut down the main power, and in the stop process of the equipment operate the equipment for no-load regularly, in order to ensure when the equipment put into use again, all
performance indexes are normal.
Special tips
① It is a precision measuring equipment, should be persons in fixed positions for machine. people without training is strictly forbidden to operate the machine.When the host is running, the operator should not stay away from the equipment.In the process of test loading or operating, if there is any abnormal situation or wrong operation, please immediately press the red emergency stop button and turn off the power.
② Fasten the nut on the T type screw of the bending bearing before the bending test, otherwise it will damage the bending clamp.
③Before the stretching test, please ensure that there is nothing in the compressed space. It is forbidden to conduct stretching test with bending device,otherwise it will cause serious damage to the equipment or personal injury accident
④ When adjusting the bending space by girder you must pay highly attention to the distance of specimen and pressure roller, it is strictly prohibited to force the specimen directly through the rising or falling of the girder , otherwise it will cause serious damage to the equipment or personal injury accident.
⑤ When the equipment needs to move or demolition, please mark the pipeline and electric circuit in advance, so that it can be properly connected when installed again; when the equipment needs hoisting, please fall the girder down to the lowest position or put a regular woods between the girder and the worktable (i.e. There must be no clearance between the girder and the worktable before hoist the host), otherwise the piston is easily taking out from the cylinder , leads to the abnormal use.
7.Appendix
Equipment diagram
Hot Products
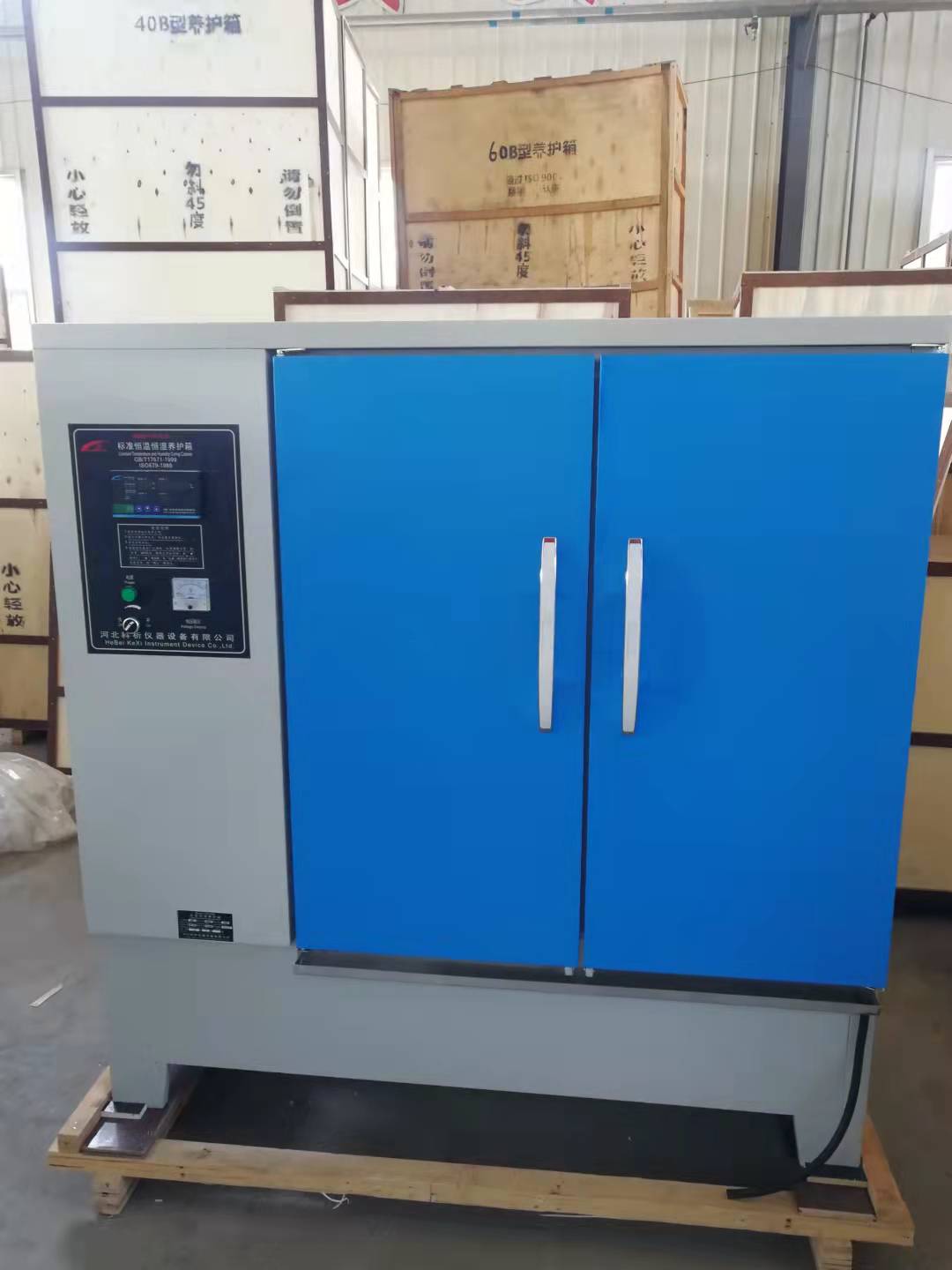
90% Humidity Curing Cabinet for Concrete
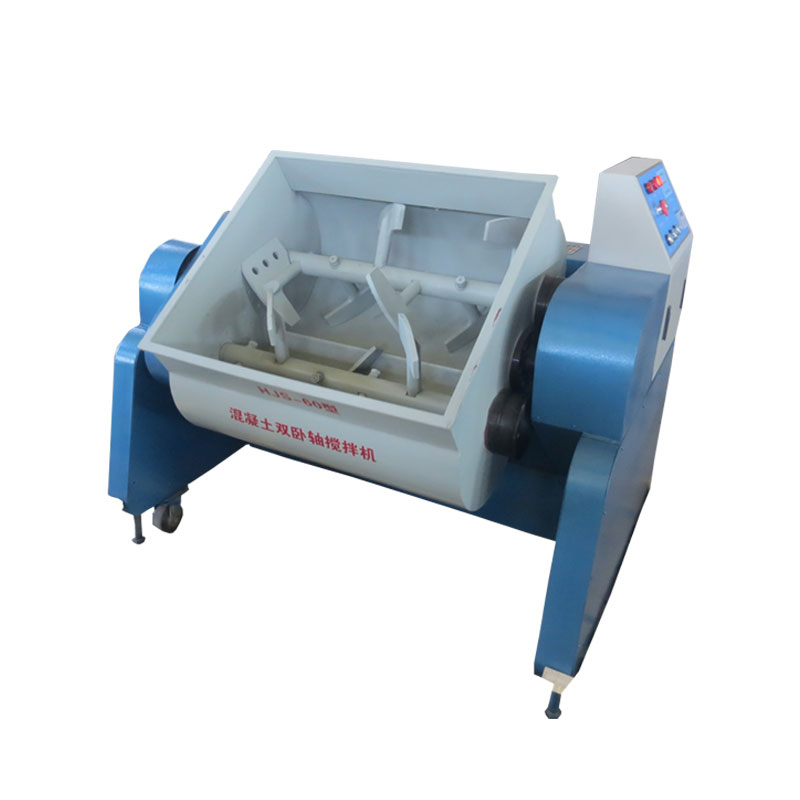
Laboratory Concrete Mixer Twin Shaft
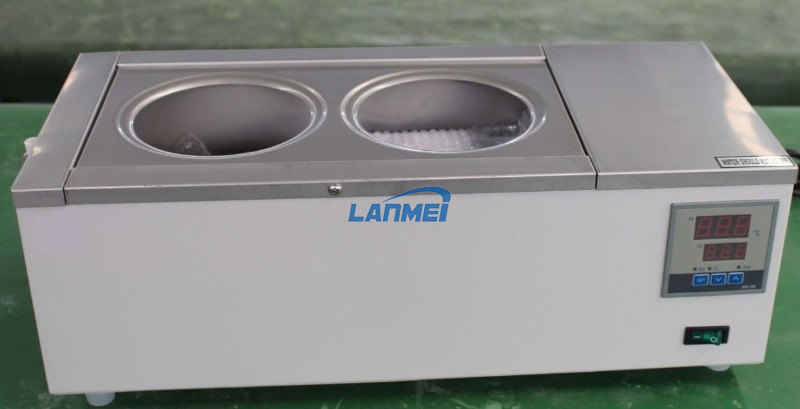
Laboratory Digital Thermostatic 2 Holes Heating Water Bath
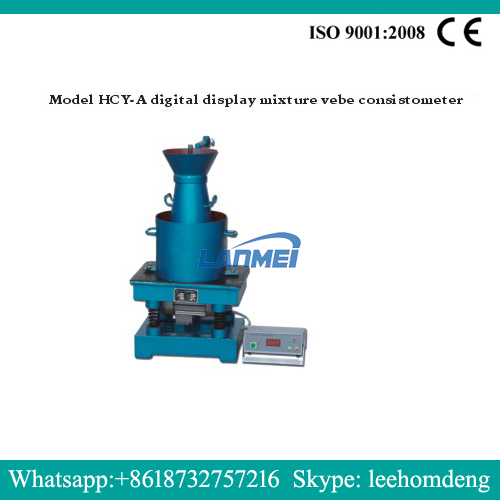
Concrete Digital Display Vebe Consistency Meter
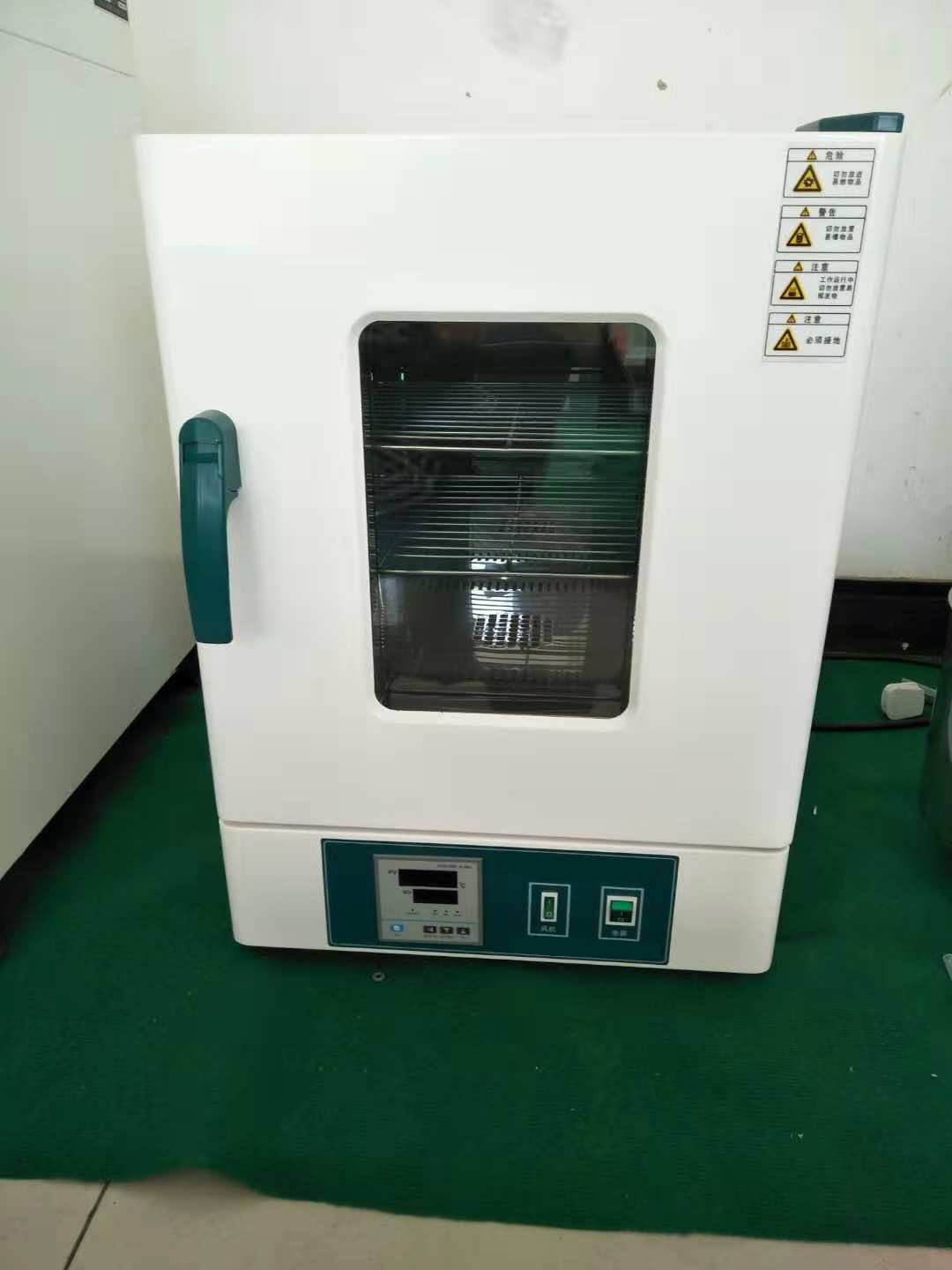
250C 300C 500C Constant Temperature desktop Drying Oven
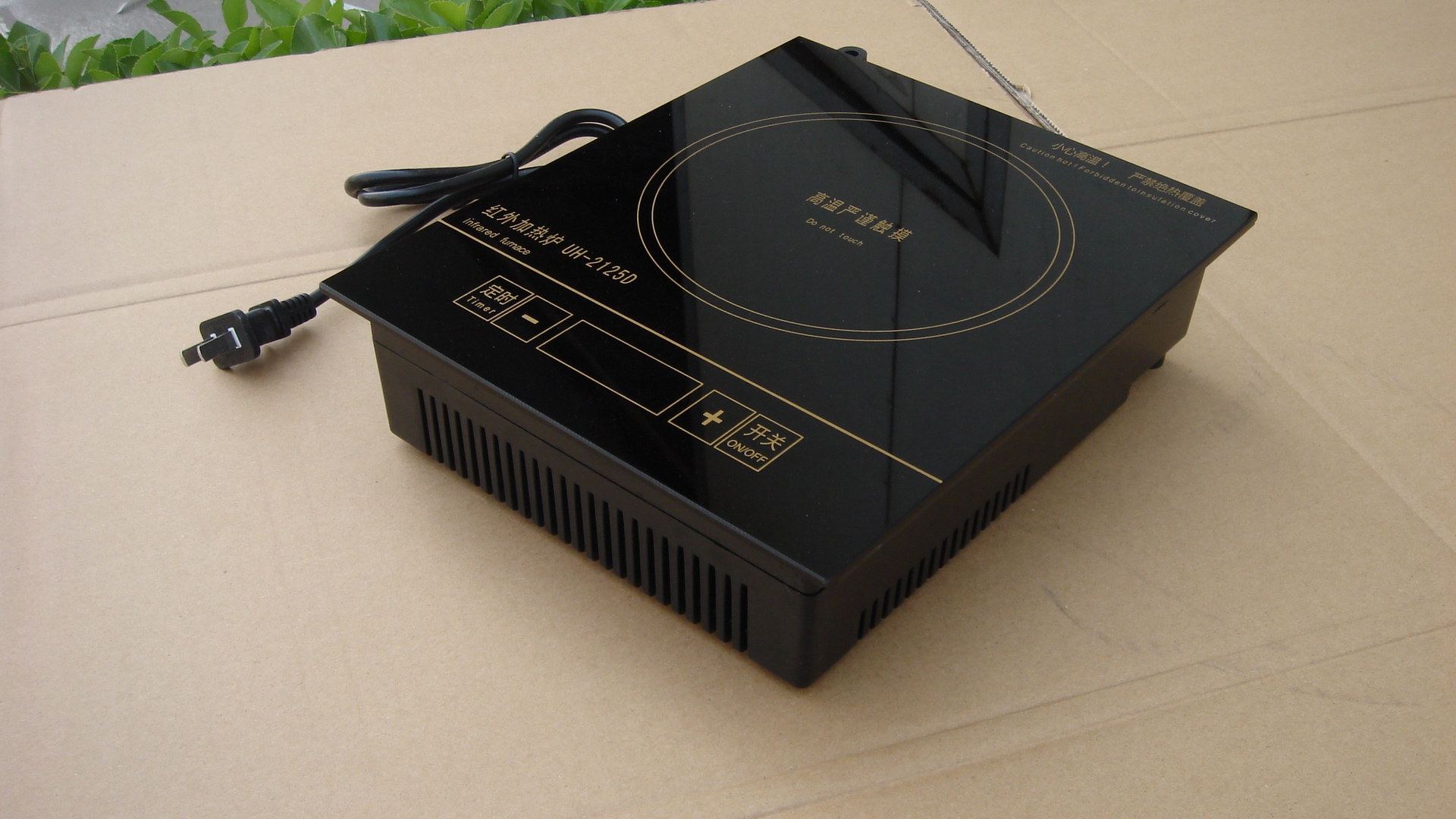
Laboratory Infrared Heating Furnace
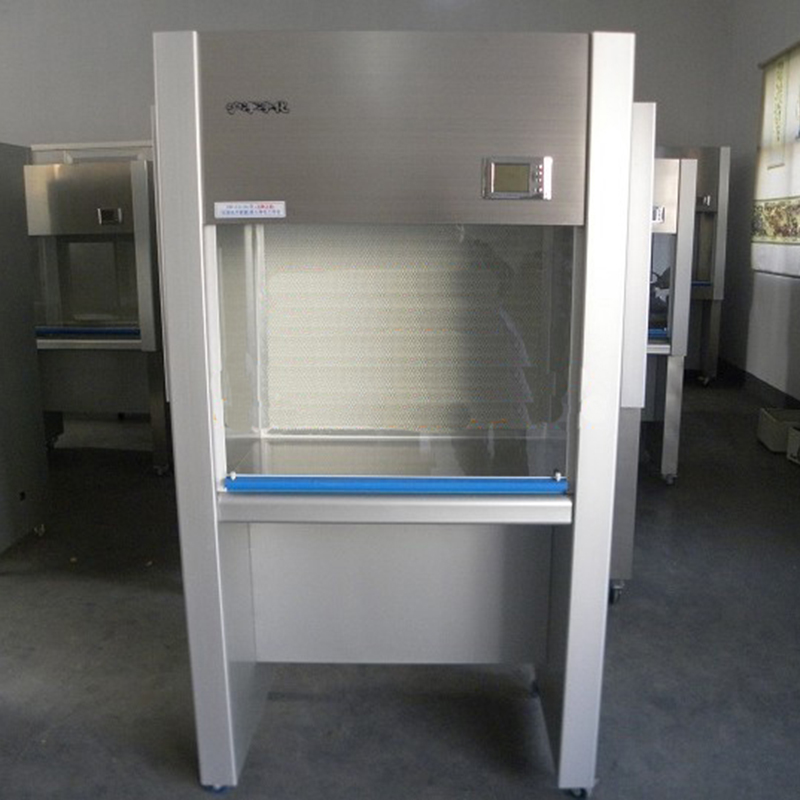
Class 100 Lab Desktop Clean Work Bench/cabinet
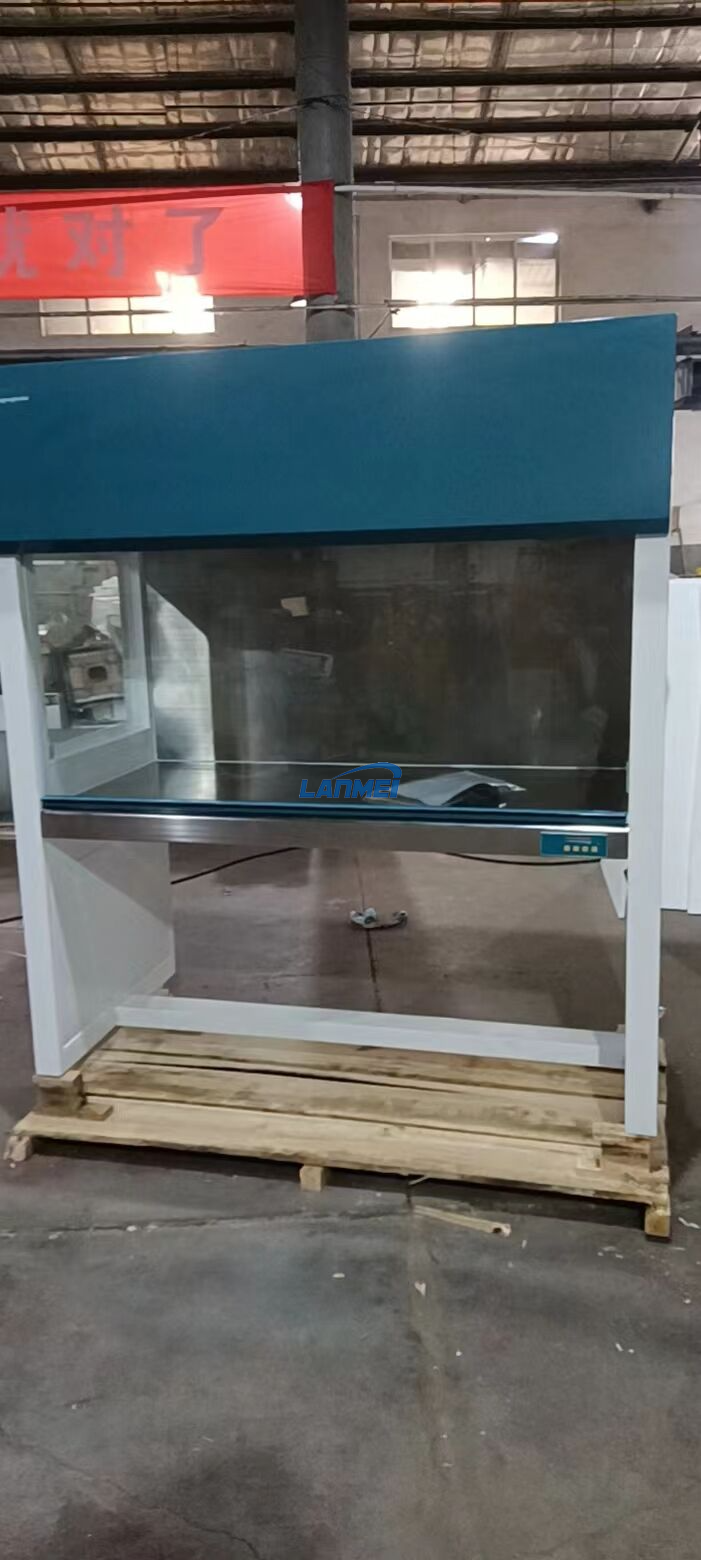
Laboratory Vertical Horizontal Laminar Air Clean Bench
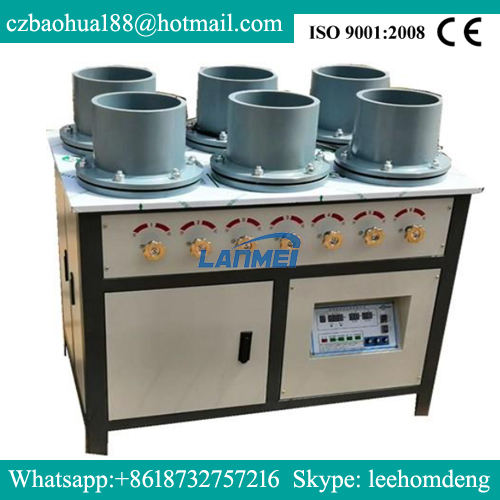
Concrete Testing Equipment for Sale
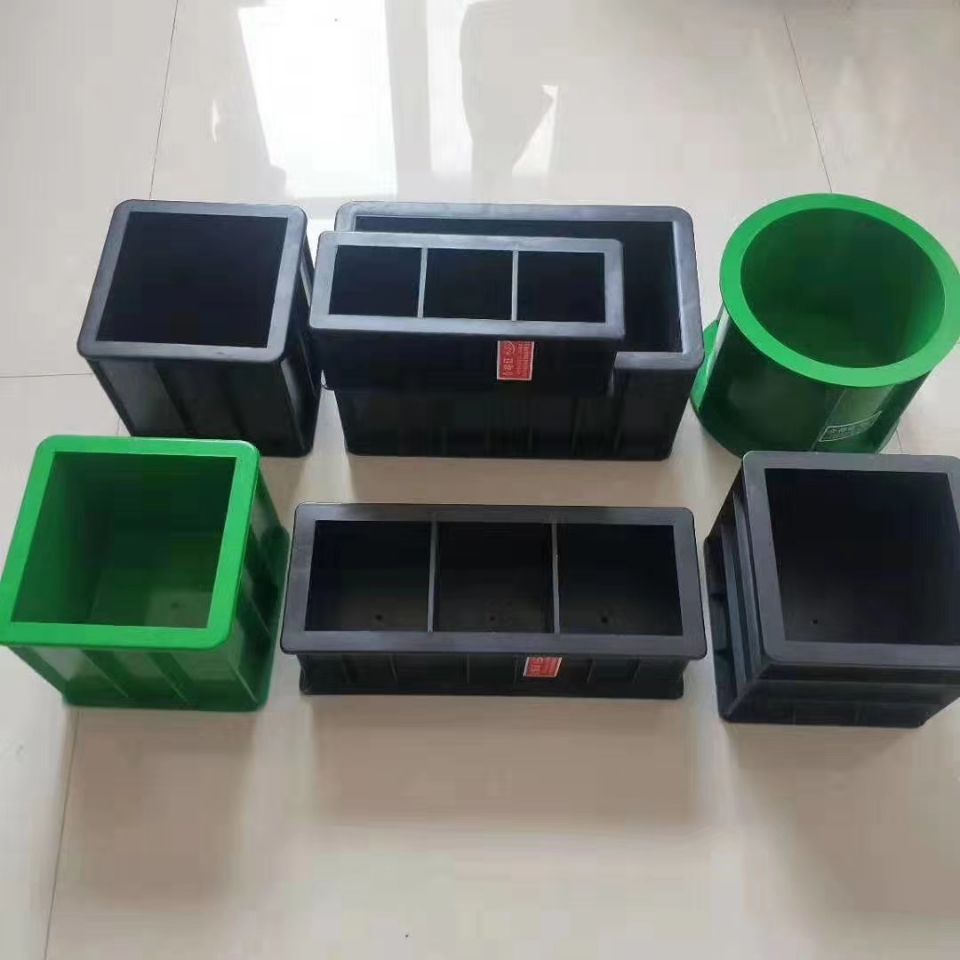
Black And Green Color Plastic Concrete Cube Test Mould
Contact us
Please feel free to give your inquiry in the form below We will reply you in 24 hours